
My commute was a little shorter this time than normal. Instead of heading off to Houston, I flew east from St. Pete and ended up on Grand Bahama Island. I managed to catch this shot of my ship on final approach as it drifted around awaiting pilots.

Fortunately the weather delayed the ship a day and I was lucky enough to get put up at a resort for the night. Bahamas cracked conch has been one of my favorite meals since I was a little kid, so it was definitely a treat to enjoy before officially joining the Spirit.

Once along side, it didn’t take long to prepare everything for drydocking. Once she was out of the water, shipyard workers swarmed to the ship to complete all the time sensitive projects. This was one of the quieter moments, which gave the chief mate and I a chance to inspect the 1000+ feet of anchor chain.

Maggy and my mom were able to catch a cruise over to Freeport for a day. They got to check out my ship and meet the crew. While Maggy knows ships all too well, my mom on the otherhand does not. It was a great experience showing her the bridge and cargo offices, the two places I spend most of my time.

Most of the shipyard consisted of managing contractors and completing final inspections. The majority of these inspections were in ballast and cargo tanks. Proper ventilation and atmospheric testing are one of the first steps prior to entry.
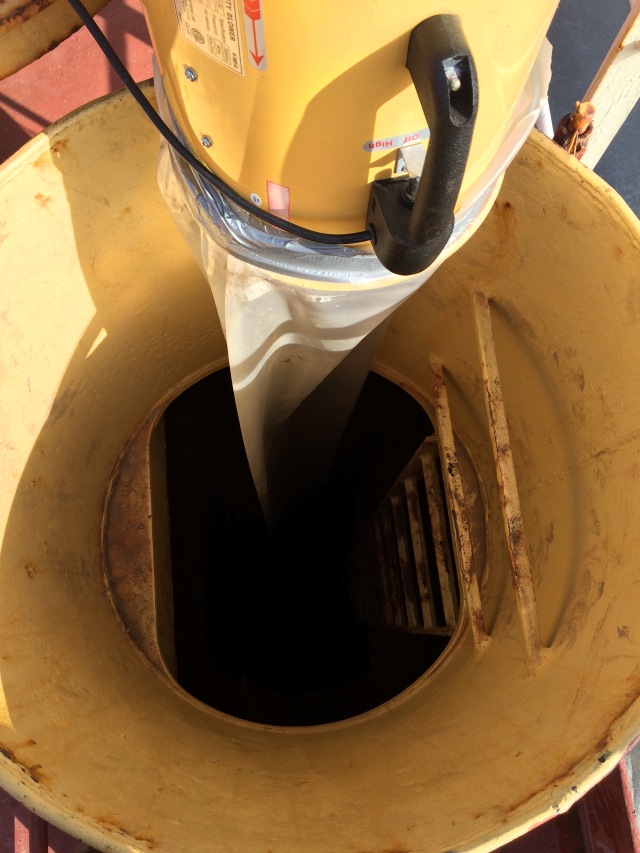
Aside from ventilation, ensuring you have adequate light is priority number two. Whenever we enter a confined space, we carry atleast two flashlights and a UHF radio to maintain communication with our standby personnel standing by the tank’s entrance,

Once at the bottom of the tank we must be very mindful of the dark and slippery surfaces we must traverse. This inspection was of a through-hull valve in the number 4 starboard ballast tank. This valve isolates the draft sensor for midship readings. Ballast tanks are normally fairly clean, although depending on the ship’s ports of call significant mud can accumulate.

In addition to my roles as third mate, I assumed the role of Keystone’s Shipyard Safety Officer. This job mostly focused on enforcement of company safety policies and daily correspondence with shipyard safety personnel.

While shipyards are mostly well planned ventures, there are some things that require a little creative thinking to accomplish. This static weight test of an engine room davit required 2500kg, yet the yard only had a 2200kg weight. After piling on some additional spare parts, two mates discuss the validity of the test with shipyard representatives.

Towards the end of the yard period a number of cruise ships joined us. Grand Bahama Shipyard is majority owned by Royal Caribbean and Carnival, so this is a regular occurence. The proximity to major cruise ports such as Miami and Ft. Lauderdale ensure a steady stream of business. Here you can see one of our small orange lifeboats compared to the twenty + cruise ships carry.

Once the yard was complete, we headed back to Houston for our first load. We were greeted by temperatures in the forties and a couple of days at anchor. Sometimes it is nice to ease into the fast pace if commercial crude trades.

Once loaded, we generally head for South West Pass and the Mississippi River. Our transit up to St. James (about 30 miles south of Baton Rouge) generally calls for half a day at anchor, which allows the crew to rest up and comply with federal work/rest requirements.

When we do get occasional down time, many of us find solice in books. Steaming to Bamboola gives a great look into the crazy dynamics of living and working with twenty other strangers from all walks of life. It was written by a journalist on a passage back in the 1970’s, so it gives a great independent perspective, even if it is a little dated.